Manual handling in the workplace involves any activity that requires lifting, carrying, pushing, or pulling objects. From warehouses to offices, proper manual handling techniques are crucial to prevent injuries and ensure a safe working environment. Every employee should have access to The Essential Manual Handling Training Checklist to minimize risk and boost workplace productivity. This checklist serves as a practical guide to ensure that staff members are equipped with the right skills to perform manual tasks safely.
Understanding the Importance of Manual Handling
Manual handling, when done incorrectly, can lead to serious injuries, such as strains, sprains, and even long-term musculoskeletal problems. The Health and Safety Executive (HSE) reports that manual handling injuries are one of the most common causes of work-related injuries. By following The Essential Manual Handling Training Checklist, employees can reduce the likelihood of such injuries and improve their overall work performance.
What is Manual Handling Training
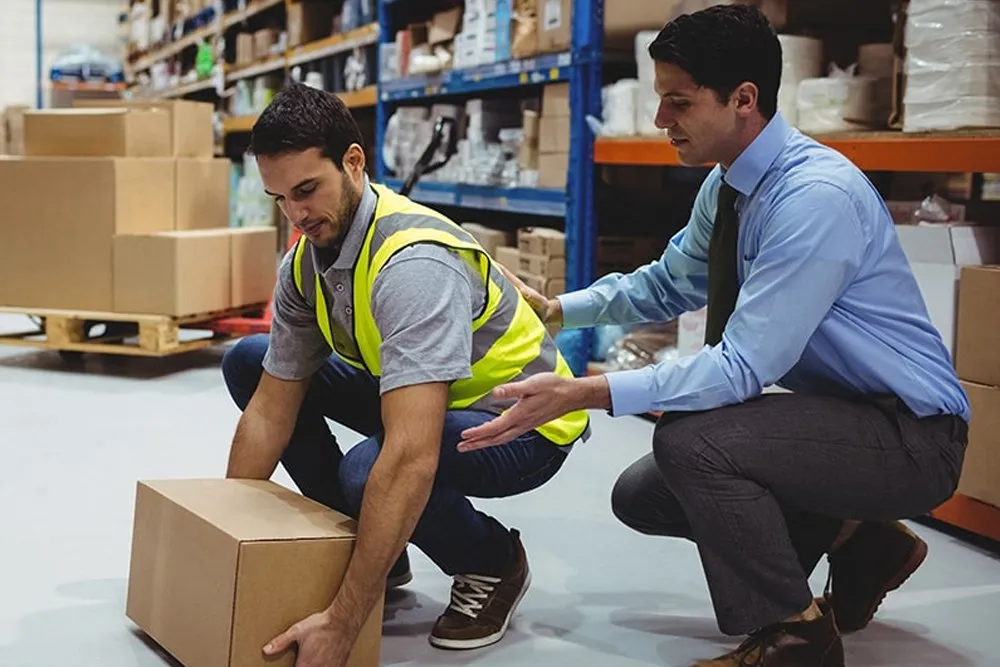
Manual handling training refers to the educational process that teaches workers how to handle objects safely, use appropriate lifting techniques, and understand the risk factors associated with physical tasks. The key to effective training lies in providing employees with the knowledge and tools to perform their tasks without putting their health at risk.
The Essential Manual Handling Training Checklist
When developing or updating manual handling training program, it is important to consider various skills and techniques. The Essential Manual Handling Training Checklist includes fundamental aspects that ensure safety while performing manual tasks in the workplace.
1. Understanding the Risks Involved
Before lifting any object, employees should be aware of the risks involved. These risks can vary from the weight and size of the object to the environment where it’s being handled. The training should highlight common risk factors, such as:
Excessive weight or unbalanced loads
Improper lifting posture
Repetitive movements
Slippery or obstructed floors
By understanding the risks, employees can identify potential hazards and avoid injuries.
2. Correct Lifting Techniques
The cornerstone of manual handling training is teaching employees how to lift objects properly. The Essential Manual Handling Training Checklist should include guidelines for correct lifting techniques, such as:
Bend the knees: Always bend your knees, not your back, to maintain a stable center of gravity.
Keep the load close: Hold the object close to your body to reduce strain on the back and arms.
Avoid twisting: Turn with your feet, not your waist, to avoid unnecessary strain on the spine.
Use both hands: When lifting an object, use both hands to distribute the weight evenly.
These techniques help to prevent unnecessary strain on the muscles, ligaments, and joints, reducing the risk of injury.
3. Assessing the Load
Before attempting any lift, it is critical to assess the load to determine whether it can be safely handled. This assessment should be a key component of manual handling training. Employees should ask themselves:
Is the load too heavy?
Is the object awkward or unbalanced?
Can it be split into smaller parts?
Are there any sharp edges or hazardous components?
If the load seems too heavy or unsafe, employees should be trained to ask for assistance or use mechanical aids, such as trolleys or forklifts.
4. Communication and Teamwork
In workplaces where heavy lifting is a common task, teamwork and communication are essential. Training employees to work together efficiently can help prevent accidents. The Essential Manual Handling Training Checklist should highlight the following:
Clear communication: Establish signals or commands that workers can use to coordinate lifting tasks.
Teamwork: Ensure all team members understand their roles and responsibilities in a lifting task.
Mutual support: Encourage staff to support each other physically and emotionally during physically demanding tasks.
Proper communication ensures that everyone is on the same page and that the task is completed safely and effectively.
5. Using Mechanical Aids
Manual handling training should emphasize the importance of using mechanical aids whenever possible. This is particularly important in environments where heavy or bulky loads are common. Workers should be trained in the proper use of:
Trolleys and carts
Forklifts
Conveyor belts
Dollies and pallet jacks
Mechanical aids reduce the physical effort required to move objects and minimize the risk of injury.
6. Proper Workstation Setup
For office workers, manual handling may involve tasks such as lifting boxes, filing documents, or setting up workstations. It’s important to train employees on how to arrange their workstations to minimize physical strain. This includes:
Using ergonomic furniture
Arranging frequently used items at waist height
Avoiding repetitive bending or stretching
A well-organized workstation minimizes the need for excessive manual handling, thus reducing injury risks.
7. Stretching and Physical Preparation
Before engaging in physically demanding tasks, workers should be encouraged to stretch and warm up. Incorporating simple stretching routines into the training ensures that muscles are loose and prepared for movement. Key areas to focus on include:
Back and shoulder stretches
Leg stretches
Wrist and hand stretches
Stretching improves flexibility and helps workers avoid injuries caused by sudden movements.
The Role of Employers in Manual Handling Training
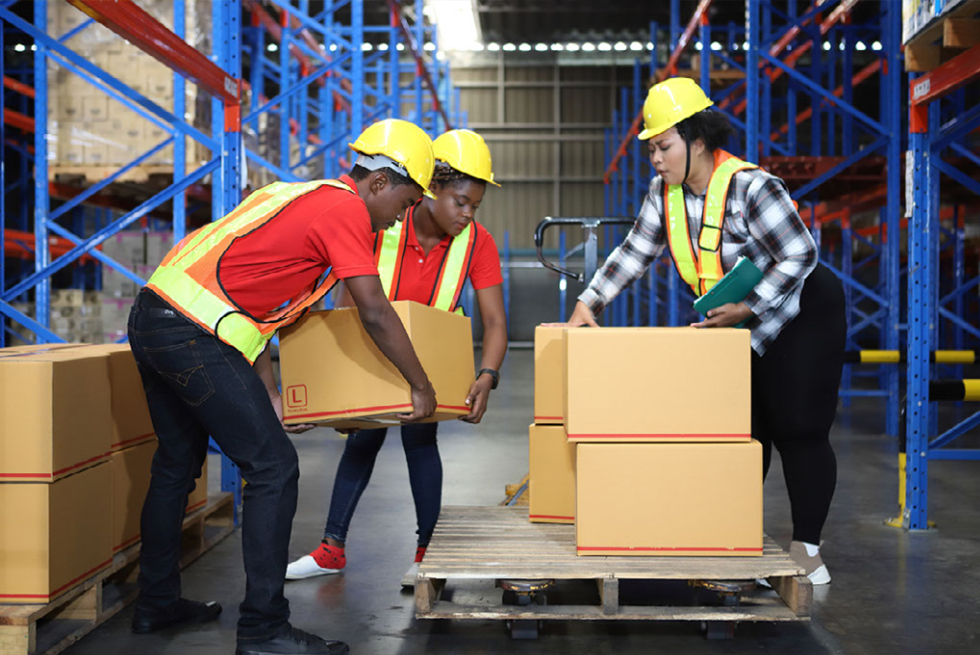
Employers have a responsibility to ensure that their employees are equipped with the knowledge and tools necessary for safe manual handling. This includes providing:
Regular training: Offer refresher courses and new training as job roles change.
Proper equipment: Ensure that mechanical aids and protective gear are readily available.
A safe environment: Keep workspaces clean and free from hazards to reduce the risk of accidents.
By fostering a culture of safety and providing employees with the right training and resources, employers can create a safer workplace for all.
Conclusion
Manual handling skills are essential to creating a safe and productive workplace. By following The Essential Manual Handling Training Checklist, employees can perform their tasks safely, reducing the risk of injury and improving overall job satisfaction. Employers who prioritize manual handling training not only protect their workers but also ensure a more efficient and harmonious work environment.
(FAQs) on Manual Handling Training
1. What is manual handling training?
Manual handling training teaches workers how to safely lift, carry, push, or pull objects without causing injury. It covers proper techniques, load assessment, and the use of mechanical aids.
2. Why is manual handling important in the workplace?
Manual handling is critical because improper lifting techniques can lead to serious injuries, such as back strain or musculoskeletal problems. Proper training minimizes these risks.
3. How often should manual handling training be conducted?
Manual handling training should be conducted during the onboarding process and regularly refreshed, especially when job roles change or new equipment is introduced.
4. What are the signs of improper manual handling?
Signs of improper manual handling include back pain, muscle soreness, joint stiffness, and limited range of motion. Employees should seek medical attention if they experience these symptoms.
5. Can mechanical aids replace manual handling?
While mechanical aids can reduce the physical strain of manual handling, they should be used in combination with proper lifting techniques. In some situations, manual handling may still be necessary.
Read Next: Winter Style Simplified: The 5 Pieces You Need This Season